Authorized Distributors of ZingaMetall Bvba in India,Sri Lanka and Nepal
M : 9372134903
E : zinga@johngalt.in / sales.zinga@johngalt.in
A : John Galt Zinga Technologies
Plot F-2, MIDC Badlapur, Dist. Thane
Maharashtra - 421503
GST - 27AAEHR6718L1ZN
ZINGA ® is an ANTI-CORROSSIVE, single-component, high-performance metallic coating that promotes a cathodic film protection system. It contains 96% zinc in its dry film, with a high content of metallic zinc (97%) and high purity (99.995%).
Zinga provides galvanisation on your structure as easily as applying paint!
Zinga can protect your galvanised or surface prepared structures for as long as 30 years*!
*Application to be done by a Zinga Approved Applicator
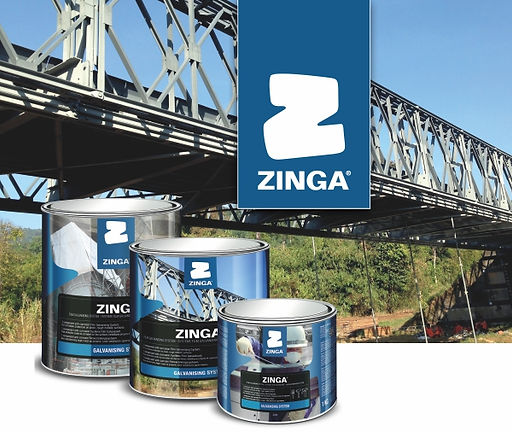
Product Range - Film Galvanising Systems
Zinga
1 pack coating containing 96% zinc and providing cathodic protection
Zinc Content - 96%(+-1%) in Dry Film (provides cathodic protection)
Zinc Purity - 99.995% pure
Colour - Steel Grey
Atmospheric temperature resistance - -40 Degree C to 150 Degree C
Atmospheric pH Resistance - 3.5 to 12.5 pH
Toxicity - Zinga is Non Toxic (Tested as per AS/NSZ 4020)
Shelf Life - Unlimited
UV Resistance - Excellent
Coverage - 3.62 m2 / kg OR 9.67 m2 / litre with 60 micron thickness
Packaging - 1 kg and 5 kg
Compatible thinner - Zingasolv

Zingalu
A 1 component high performance standalone organic zinc rich coating
Zinc Content - 90% ultra pure Zinc + 4% Aluminum Flakes in Dry Film (provides cathodic protection)
Zinc Purity - 99.995% pure
Colour - Grey with Aluminum Shine
Atmospheric temperature resistance - -40 Degree C to 150 Degree C
Atmospheric pH Resistance - 3.5 to 12.5 pH
Toxicity - Zinga is Non Toxic (Tested as per AS/NSZ 4020)
Shelf Life - 2 years in original unopened package
UV Resistance - Excellent
Coverage - 4.26 m2 / kg OR 10.5 m2 / litre with 60 micron thickness
Packaging - 5 kg
Compatible thinner - Zingasolv

AquaZinga
A 2 pack 100% water based anti-corrosive system based on inorganic zinc silicates.
Excellent Abrasion Resistance & withstands severe corrosive environment
Zinc Content - 92% (+-2%) in Dry Film (provides cathodic protection)
Zinc Purity - 99.995% pure
Colour - Steel Grey
Atmospheric temperature resistance - -90 Degree C to 600 Degree C
Atmospheric pH Resistance - 5.5 to 9.5 pH
Toxicity - Zinga is Non Toxic (Tested as per AS/NSZ 4020)
Shelf Life - 12 months if unopened
UV Resistance - Excellent
Coverage - 3.62 m2 / kg OR 9.67 m2 / litre for 60 microns
Packaging - 10 kg - 7.6 kg powder and 2.4 kg binder
Compatible thinner - No Thinner needed

Zinga Tarfree - Topcoat
A 1 pack moisture curing polyurethane paint. It exhibits excellent water and corrosion resistance (thanks to the MIO particles) and outstanding chemical resistance. These properties make Zingatarfree the ideal product to replace normal coal tar products. Zingatarfree is recommended for use in duplex systems as a topcoat with ZINGA for application on structures in immersion or embedded in soil.
​
​
Colour - Black
Shelf Life - 2 years if unopened
UV Resistance - Excellent
Coverage - For 90 microns, 7.6 square meter per litre
Packaging - 5 litre

Zinga Spray and Zingalu Spray
Zinc Content - 96%(+-1%) in Dry Film
Zinc Purity - 99.995% pure
Colour - Steel Grey / Grey with Aluminum Shine
Atmospheric temperature resistance - -40 Degree C to 150 Degree C
Atmospheric pH Resistance - 3.5 to 12.5 pH
Toxicity - Zinga is Non Toxic (Tested as per AS/NSZ 4020)
Shelf Life - 1 year
UV Resistance - Excellent
Coverage - For 40 μm, DFT: 3 m²/500ml

How does it work?
When two different metals come in contact with each other in presence of an electrolyte (e.g. water), they form a galvanic cell in which the lesser noble metal (e.g. Zn) corrodes in favour of the more noble metal (e.g. steel). This electrochemical reaction is the base for the complex field that is cathodic protection.
​
Galvanic, cathodic protection, or active protection, arises from zinc (the anode) sacrificing itself in favour of the base metal -steel (the cathode) with the resulting flow of electrons preventing steel corrosion. In this way the protection of the metal is guaranteed, even when the zinc layer is slightly damaged.
​
Other well-established methods of cathodic protection include hot-dip galvanising (HDG) and zinc thermal spraying, both of which exhibit a constant sacrificial rate of the zinc layer.
With ZINGA the sacrificial rate reduces dramatically after the zinc layer has oxidised and the natural porosity has been filled with zinc salts. Additionally the zinc particles within the ZINGA layer are protected by the organic binder without adversely affecting the electrical conductivity. This enables ZINGA to create nearly the same galvanic potential between the zinc and the steel as hot dip galvanising but with a lower rate of zinc loss because, put simply, the binder acts as a “corrosion inhibitor” to the zinc.

About John Galt International
Founded in 1978, John Galt International is a Total Quality Management certified heavy engineering company.
Our expertise lies in design, manufacturing and supply of process equipment such as
​
-
Storage tanks and bullets, Pressure Vessels and Reactors, Heat Exchangers, Distillation Columns, Boilers
-
Material Handling Equipment such as E.O.T Cranes, Stackers, Reclaimers and Wagon Tipplers, Conveyors and Frames
​
We have a 15000 sq meter manufacturing plant in Badlapur, Maharashtra
About John Galt Zinga Technologies
John Galt Zinga Technologies is the authorised all India Distributor of ZingaMetall BvBa. We are the principal importers of Zinga products in India.
Zinga is the market leader in COld Galvanizing.
Team

R.K. BHATIA
Founding Partner
Mr. R.K. Bhatia is a graduate in Mechanical Engineering and post graduation in Business Management. He has more than 45 years of Industrial experience, starting his career with companies like Larsen & Toubro and Voltas. He has received many recognitions from Industrial Forums for his contribution in the field of manufacturing. He manages operations and finances for the group companies.
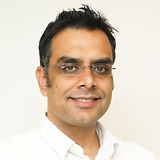
ABHAY BHATIA
Partner
Abhay graduated in Computer Engineering in 2007, following which he worked in various roles at John Galt. In 2013, he completed his MBA in General Management and Marketing from the Indian School of Business. Since then, Abhay heads sales, marketing and strategy